Procesul Haber-Bosch
Procesul Haber-Bosch este un produs chimic industrial pe scară largă proces de sinteză a amoniacului . Acesta poartă numele chimiștilor germani Fritz Haber și Carl Bosch , care au dezvoltat procesul la începutul secolului al XX-lea. Etapa centrală a procesului, sinteza amoniacului din azot atmosferic și hidrogen , este realizată pe un catalizator care conține fier la presiuni de aproximativ 150 până la 350 bari și temperaturi de aproximativ 400 până la 500 ° C. Fiind un proces chimic major cu o producție de peste 150 de milioane de tone în 2017, acoperă mai mult de 99% din producția globală de amoniac.
Amoniacul este o substanță chimică care este utilizată în principal pentru producerea de uree , azotat de amoniu , sulfat de amoniu și fosfați de amoniu . Aceste substanțe sunt utilizate ca îngrășăminte și contribuie la nutriția unei mari părți a populației lumii. Amoniacul este, de asemenea, utilizat la fabricarea explozivilor și a altor substanțe chimice care conțin azot. Reducerea catalitică selectivă utilizând amoniac în denitrificarea gazelor de ardere pentru conversia nocive a oxizilor de azot în azot și apă. Amoniacul a fost, de asemenea, utilizat ca agent frigorific ecologic și eficient din punct de vedere energetic din 1876 .
Realizările științifice pentru realizarea acestui proces au fost, pe de o parte, investigarea reacției chimice subiacente de către Fritz Haber și Walther Nernst , pe de altă parte, căutarea sistematică a catalizatorilor adecvați de către Alwin Mittasch , precum și clarificarea ingineriei fundamentale a proceselor probleme pentru procesele de înaltă presiune de Carl Bosch. În legătură cu procesul Haber-Bosch, Fundația Nobel i-a acordat Premiul Nobel pentru chimie lui Fritz Haber în 1918 , lui Carl Bosch în 1931 și lui Gerhard Ertl în 2007 , care a găsit explicația teoretică completă a mecanismului de formare a amoniacului.
poveste
Pâine făcută din aer
Din lucrările lui Justus von Liebig, se știe încă de la mijlocul secolului al XIX-lea că absorbția compușilor de azot este o bază pentru creșterea culturilor. Compușii necesari de azot au fost furnizați terenului arabil prin gunoi de grajd, compost sau printr-o rotație specifică a culturilor . Datorită creșterii rapide a populației mondiale în secolul al XIX-lea, cererea mare asociată de îngrășăminte cu azot nu ar mai putea fi satisfăcută de aparițiile naturale de guano sau azotat ale Chile, de exemplu, sau de surse tehnice, cum ar fi gazul de cocserie . Pentru a atrage atenția asupra acestui fapt, chimistul britanic William Crookes a ținut un discurs foarte apreciat în fața Asociației Britanice pentru Avansarea Științei din Bristol în iunie 1898 . În el, el a declarat că până în 1918 cererea de compuși de azot va depăși cu mult oferta și lumea occidentală a fost amenințată cu o foamete de proporții neimaginate. El a continuat spunând că singura soluție la această problemă a fost fixarea chimică a azotului din aer. El a numit implementarea tehnică a acestui proces una dintre marile provocări pentru chimiștii din timpul său. Încercarea de a lega azotul atmosferic într-o substanță chimică pe care plantele o pot absorbi, cunoscută sub expresia „Pâine din aer”, a avansat apoi pentru a deveni unul dintre punctele focale ale cercetării chimice la acea vreme.
Evoluții timpurii

O primă descoperire în fixarea azotului atmosferic a venit în 1898 odată cu prepararea cianamidei de calciu conform procesului Frank Caro , în care carbura de calciu absoarbe azotul atmosferic la temperaturi ridicate și astfel îl fixează. Hidroliza cianamidei de calciu furnizează amoniac și carbonat de calciu . Deși s-au acumulat capacități mari pentru producerea cianamidei de calciu, procesul nu a fost competitiv pe termen lung din cauza necesității ridicate de energie de aproximativ 190 gigajouli pe tonă de amoniac.
În 1900, Wilhelm Ostwald a înregistrat un brevet pentru „producerea de amoniac și compuși de amoniac din azot liber și hidrogen”, deoarece aparent a reușit să producă amoniac catalitic din elemente. Încă din 1903, producătorul de explozivi Rottweiler, Max Duttenhofer, a publicat avertismentul lui Ostwald cu privire la un embargo asupra salpetrului în caz de război în „mercurul șvab”. Ostwald și-a retras brevetul după ce Bosch a dovedit că amoniacul produs provine din nitrura de fier a catalizatorului utilizat.
Procesul Birkeland-Eyde , care a fost dezvoltat de omul de știință norvegian Kristian Birkeland și partenerul său de afaceri Sam Eyde și pus în funcțiune în 1903, a fixat azotul atmosferic oxidându-l direct în oxid nitric folosind un arc electric . La răcire și oxidare suplimentară, s-a format oxid azotat , care a reacționat la acidul azotic prin absorbție în apă. Eficiența energetică scăzută a dus în curând la deplasarea procesului.
Muncă de bază
În 1904 Fritz Haber, care la acea vreme lucra ca profesor asociat de chimie tehnică în Karlsruhe , a început să se ocupe de principiile chimice ale sintezei amoniacului. Constanta de echilibru găsită pentru sinteza amoniacului din elementele azot și hidrogen a corespuns unui randament mai mic de 0,01 procente la o temperatură de 1000 ° C și presiune normală și, prin urmare, a fost prea scăzută pentru a implementa un proces tehnic. Haber era conștient de faptul că presiunile mai mari vor duce la randamente mai bune, dar, din cauza problemelor tehnice anticipate, și-a oprit temporar cercetările în acest domeniu. Doar o discuție științifică cu Walther Nernst despre constanta de echilibru a sintezei amoniacului bazată pe teorema lui Nernst l-a determinat pe Haber să-și continue activitatea. În urma unor cercetări suplimentare, el a considerat că transferul către tehnologie va fi posibil doar la temperaturi sub 300 ° C și numai cu un catalizator adecvat . La scurt timp după aceea, a reușit să-l pună în practică cu ajutorul unui catalizator pe bază de osmiu .
La 13 octombrie 1908, Haber a solicitat Oficiului Imperial de Brevete din Berlin protecția brevetului pentru o „metodă de preparare sintetică a amoniacului din elemente”, care a fost acordată la 8 iunie 1911 cu brevetul nr. 235.421. Din moment ce lucra acum cu BASF , a acordat companiei brevetul pentru uz comercial.
realizare tehnică
Aprovizionarea cu hidrogen a materiei prime, în special, care până atunci era disponibilă doar în cantități mai mari în electroliză clor-alcalină , a necesitat procese complet noi. De asemenea, pentru construcția reactoarelor chimice necesare pentru sinteza amoniacului , în care hidrogenul putea fi controlat la presiuni și temperaturi ridicate, până atunci nu existau referințe în tehnologie. Carl Bosch și Fritz Haber au dezvoltat apoi noi soluții în multe domenii ale chimiei tehnice și ale construcției reactoarelor.
Datorită numărului mare de specialiști necesari implementării producției la scară industrială, Bosch a fondat o divizie interdisciplinară de inginerie chimică în care inginerii mecanici și chimiștii au lucrat împreună. Deoarece oțelul utilizat inițial pentru construcția reactorului erodate de hidrogen , care a difuzat în atomically, una dintre sarcinile noului zona de lucru a fost de a cerceta materialul daune cauzate de decarburare a oțelurilor carbon . Acest lucru a dus în cele din urmă la dezvoltarea oțelurilor cu crom-nichel din aliaj înalt, care rezistă la atacul de hidrogen la temperaturile și presiunile de reacție necesare. În special, procesul de înfășurare Schierenbeck dezvoltat de Julius Schierenbeck , în care mai multe straturi de bandă de metal fierbinte au fost micșorate pe un tub central rezistent chimic, a făcut posibilă construirea de reactoare de înaltă presiune mai mari și mai sigure. În același timp, Alwin Mittasch a dezvoltat și testat în jur de 3000 de catalizatori diferiți pe bază de oxid de fier cu diverse substanțe care accelerează conversia, pe care le-a numit activatori sau promotori , în 20.000 de experimente . Catalizatorul utilizat în 2015 a corespuns în mare măsură celui dezvoltat de Mittasch.
În 1913, BASF a comandat pentru prima dată o fabrică bazată pe procesul Haber-Bosch la uzina Ludwigshafen-Oppau . Capacitatea uzinei era inițial de 30 de tone pe zi. Încă din 1914, șeful statului major german Erich von Falkenhayn a împins dezvoltarea în continuare a procesului până când acesta ar putea fi utilizat la scară industrială largă , după care Bosch a făcut așa-numita promisiune a salpetrului . Acesta a fost un contract pentru livrarea nitraților cu garanții de cumpărare și cu sprijin financiar de la Reich pentru construcția de instalații adecvate. Acest lucru ar trebui să permită azotatului de amoniu ca bază pentru explozibilii militari să fie produși în cantități suficiente, fără săpăturile naturale utilizate în alt mod. La scurt timp după aceea, procesul Haber-Bosch a reușit să producă în mod corespunzător cantități mari de material de război. Acest lucru a permis Reich-ului german, întrerupt din sursele de azot, cum ar fi azotatul Chile, de blocada navală britanică , să-și mențină producția de muniție și îngrășăminte în timpul primului război mondial și să evite colapsul economic. Pe lângă fabrica de mari dimensiuni din Oppau lângă Ludwigshafen , altele din Leuna și Bitterfeld au fost operate de BASF și, după fuziunea în marea corporație germană, de IG Farben .
După primul război mondial
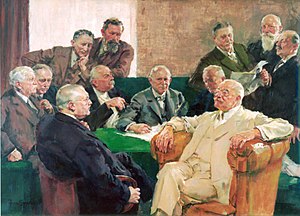
După război, puterea victorioasă Franța a obligat BASF prin intermediul unui acord să predea toate brevetele și experiența legată de proces și să sprijine construcția unei fabrici corespunzătoare în Toulouse . În Anglia, Italia și alte țări au fost construite în același timp plante suplimentare de amoniac. Acest proiect de construcție s-a bazat fie pe o licență de la BASF, fie pe o variantă de proces cu parametri de proces modificați, inclusiv procesul Casale și procesul Mont-Cenis cu catalizator modificat.
IG Farben a fost fondat în perioada dintre cele două războaie mondiale, cu Carl Bosch ca prim-director executiv. Încă din 1926, capitalizarea de piață a companiei, care acum are 100.000 de angajați, era de aproximativ 1,4 miliarde de Reichsmarks . Criza economică globală care a început odată cu prăbușirea pieței bursiere din New York din octombrie 1929 a redus considerabil cererea de amoniac sintetic. Producția din Germania, care ajunsese deja la un volum anual de peste 800.000 de tone, a scăzut apoi sub 500.000 de tone, iar veniturile IG Farben au fost reduse la jumătate. Cu toate acestea, IG Farben a rămas cel mai mare producător de amoniac din lume până în 1930; Sinteza amoniacului a reprezentat 65% din profitul total.
Embargo-ul de import pentru îngrășăminte cu azot emis de cabinetul Brüning a permis IG Farben să ridice din nou prețurile îngrășămintelor sintetice. După preluarea puterii de către Hitler, regimul nazist a preluat controlul asupra IG Farben. Ca răspuns la presiunile exercitate de regimul nazist, Bosch și -a dat demisia din funcția de consiliu în 1935, care a revenit membrului NSDAP și liderului economic militar Hermann Schmitz . În 1940, producția de amoniac în Germania a ajuns deja la un milion de tone pe an. Ca urmare a cererii în continuă creștere pentru amoniac și produsele sale secundare, au fost create reactoare din ce în ce mai puternice.
După al doilea război mondial
Disponibilitatea crescândă a țițeiului ieftin și procesele de gazeificare care reduc costurile , de exemplu, prin oxidarea parțială a fracțiilor de țiței au făcut posibilă înființarea centralelor Haber-Bosch în întreaga lume după cel de-al doilea război mondial. Oxidarea parțială dezvoltată inițial de IG Farben a fost îmbunătățită de compania Imperial Chemical Industries (ICI) și extinsă pentru a include oxidarea naftei , ceea ce a făcut ca materiile prime ale procesului să fie mai ieftine în anii 1950 și 1960.
Companiile de inginerie, cum ar fi MW Kellogg, au dezvoltat ulterior centrale la scară largă mai eficiente din punct de vedere energetic și, prin urmare, mai rentabile, cu un singur reactor, ceea ce a dus la o creștere a capacității centralei la nivel mondial . Concurența crescândă și presiunea ridicată a costurilor au pregătit în cele din urmă calea pentru procesul LCA de la ICI și procesul KAAP de la Kellogg, Brown & Root , în care a fost utilizat pentru prima dată un catalizator de ruteniu .
materie prima
Amoniacul este creat într-o reacție de echilibru din elementele hidrogen și azot conform ecuației
- ,
prin care azotul necesar este preluat din aerul ambiant. Oxigenul, care este, de asemenea, conținut în aer, dar este nedorit, a fost transformat mai întâi în apă prin reducere cu hidrogen și astfel separat; procesul Fauser a folosit azotul, care nu a fost transformat în timpul arderii amoniacului cu aerul, ca materie primă. Mai târziu, producția de azot prin separarea aerului în conformitate cu procesul Linde s-a dovedit a fi mai economică.
Cea mai mare parte a costurilor de producție este cauzată de achiziționarea de hidrogen, care a fost inițial obținută din electroliza clor-alcalină costisitoare . Cu gazul natural, țițeiul, cărbunele și produsele de electroliză ale apei, s-au adăugat ulterior alte surse pentru producerea hidrogenului.
BASF utilizează gaz de apă pe baza de gazeificare a cărbunelui a lignitului cu ajutorul unui generator de Winkler ca sursă primară. Hidrogenul se obține prin reacția aburului cu cocs strălucitor. Aerul furnizat este dozat în așa fel încât oxigenul să fie complet transformat în monoxid de carbon . Azotul necesar pentru sinteza ulterioară de amoniac a rămas în gazul apei. Monoxidul de carbon a fost apoi transformat în dioxid de carbon ușor de îndepărtat sau utilizat într-o reacție de deplasare apă-gaz pentru a furniza hidrogen suplimentar. În 2008, aproximativ 18% din hidrogenul produs la nivel mondial a fost produs din cărbune ca materie primă.
Deși gazul natural nu era încă disponibil pentru BASF ca materie primă pentru producerea de hidrogen în anii 1920, Carl Bosch a inițiat dezvoltarea reformării cu abur a metanului , care va deveni ulterior o parte importantă a procesului. Georg Schiller a realizat o descoperire pentru IG Farben, care a reușit să reformeze metanul cu abur folosind un catalizator de oxid de nichel. Standard Oil din New Jersey , a fost acordată o licență pentru producerea hidrogenului prin reformarea cu abur la uzina din 1931 Baton Rouge din Louisiana a început. Reformarea cu abur a gazelor naturale a reprezentat aproximativ 48% din producția globală de hidrogen în 2014, din care aproximativ 60% au folosit procesul Haber-Bosch.
O altă metodă posibilă de producere a hidrogenului este oxidarea parțială . În acest caz, gazul natural sau originea petrolului sunt hidrocarburi gazificate cu oxigen și abur într-un reactor deschis fără catalizator la aproximativ 1100 ° C și gazul de sinteză procesat în continuare ca la reformarea aburului. Cele mai mari hidrocarburi din petrol au contribuit cu 30% la producția anuală de hidrogen în 2008.
Hidrogenul poate fi obținut și prin electroliza apei. Ca urmare, apa este descompusă în hidrogen (H 2 ) și oxigen (O 2 ) folosind energie electrică . Acest proces este economic doar dacă este disponibilă o energie electrică ieftină, de exemplu din hidroenergie . În 2008, electroliza a reprezentat aproximativ patru la sută din producția de hidrogen.
Odată cu apariția capacităților de platformare în Statele Unite la mijlocul anilor 1950, a devenit disponibilă o sursă petrochimică de hidrogen care, în 1956, a furnizat aproximativ 11% din hidrogenul necesar pentru sinteza amoniacului în Statele Unite. Alte procese de rafinărie, cum ar fi hidrodesulfurarea și hidrocracarea, au folosit ulterior hidrogenul produs.
catalizator
Pentru a reduce energia de activare și creșterea asociată a vitezei de reacție , o substanță suplimentară, catalizatorul , este utilizată în multe procese chimice , care nu este consumată în timpul reacției. Dacă starea fizică a catalizatorului diferă de cea a substanțelor reale care reacționează între ele, acesta este un catalizator eterogen. Acesta este și cazul procesului Haber-Bosch, în care fierul fin divizat pe un purtător de oxid de fier în formă solidă servește drept catalizator într-un amestec de gaze care reacționează. Acest catalizator eterogen, cunoscut și sub numele de „contact”, este creat în timpul reacției dintr-un alt material introdus anterior în reactor, „precursorul catalizatorului” sau „contactul precursorului ”.
Catalizator de fier

Catalizatorul de fier eterogen este o formă catalitică foarte activă de α-fier cubic centrat pe corp și este produs prin reducerea chimică dintr-o formă specială de fier oxidat, magnetitul (Fe 3 O 4 ). Efectul catalizatorului este sporit de promotorii oxidici care au fost adăugați în prealabil la magnetit. În cazul sintezei de amoniac, acestea includ, de exemplu, oxid de aluminiu , oxid de potasiu , oxid de calciu și oxid de magneziu .
Producerea contactului de magnetit necesar necesită un proces special de topire în care materiile prime utilizate trebuie să fie lipsite de otrăvuri de catalizator și suplimentele promotorului trebuie să fie distribuite uniform în topitura magnetitei. Răcirea rapidă a topiturii magnetitei, care are o temperatură de aproximativ 3500 ° C, formează catalizatorul dorit cu activitate ridicată , ceea ce reduce rezistența la abraziune. În ciuda acestui dezavantaj, metoda de răcire rapidă este adesea preferată în practică.
Reducerea magnetita precursor de catalizator la α-fier se realizează cu gaz de sinteză , în mod direct în instalația de producție. Reducerea magnetitei are loc inițial prin nivelul wüstitei (FeO), astfel încât contactul se formează cu un miez din magnetită, care este înconjurat de o carcasă din wüstite. Reducerea suplimentară a fazei magnetită și wustită duce la formarea a-fierului, care împreună cu promotorii formează învelișul exterior. Procesele implicate sunt complexe și depind de temperatura de reducere. Deoarece wustita disproporționată la temperaturi mai scăzute într-o fază de fier și magnetită, la temperaturi mai ridicate este reducerea magnetitei la fierul Wüstit- și procesul dominant.
A-fierul formează cristalite primare cu un diametru de aproximativ 30 nanometri . Acestea formează un sistem de pori bimodali cu diametre de pori de aproximativ 10 nanometri, care rezultă din reducerea fazei magnetite, sau de la 25 la 50 nanometri, care rezultă din reducerea fazei wüstite. Cu excepția oxidului de cobalt, promotorii nu sunt reduși.
Când oxidul de fier este redus cu gaz de sinteză, vaporii de apă sunt produși ca subprodus. Acest vapor de apă trebuie luat în considerare pentru o calitate optimă a catalizatorului. Dacă acesta intră în contact cu fierul fin divizat, acest lucru duce, în special în legătură cu temperaturi ridicate, la îmbătrânirea prematură a catalizatorului datorită recristalizării . Din acest motiv, presiunea de vapori a apei din amestecul gazos format în timpul formării catalizatorului este menținută cât mai scăzută posibil, valorile sub 3 gm- 3 fiind urmărite. Din acest motiv, reducerea se efectuează la schimburi mari de gaze , presiune scăzută și temperaturi scăzute. Naturii exoterme a formării amoniacului asigură o creștere treptată a temperaturii.
Reducerea catalizatorului sau a precursorului proaspăt, complet oxidat, până la atingerea capacității maxime durează patru până la zece zile. Faza wüstite este mai rapidă decât faza magnetită (Fe 3 O 4 ) și este redusă la temperaturi mai scăzute. După investigații cinetice, microscopice și spectroscopice cu raze X detaliate, s-a putut demonstra că wüstita este prima care se transformă în fier metalic. Aceasta duce la o neomogenitate (gradient) a densității ionilor de fier (II) , ca urmare a căreia se difuzează de la magnetit prin wüstită la interfață și precipită acolo ca nuclee de fier.
În practica tehnică, catalizatorii pre-reduși și stabilizați au câștigat o cotă de piață semnificativă . Au deja structura porilor complet dezvoltată , dar au fost oxidate din nou la suprafață după producție și, prin urmare, nu mai sunt piroforice . Reactivarea acestor catalizatori prereduși durează doar 30 până la 40 de ore în loc de perioadele obișnuite de câteva zile. În plus față de timpul scurt de pornire, acestea au și alte avantaje datorită rezistenței la apă mai mari și greutății mai mici.
Compoziția unui contact | % Fier | % Potasiu | % Aluminiu | % Calciu | % Oxigen |
---|---|---|---|---|---|
Compoziția volumului | 40,5 | 0,35 | 2.0 | 1.7 | 53.2 |
Compoziția suprafeței înainte de reducere | 8.6 | 36.1 | 10.7 | 4.7 | 40.0 |
Compoziția suprafeței după reducere | 11.0 | 27.0 | 17.0 | 4.0 | 41,0 |
Catalizatori, altele decât fierul
De la introducerea industrială a procesului Haber-Bosch, s-au făcut multe eforturi pentru îmbunătățirea acestuia, rezultând progrese semnificative. Cu toate acestea, în îmbunătățirea catalizatorului pentru sinteza amoniacului, nu s-au înregistrat progrese semnificative de mult timp de la anii 1920.
Ca parte a căutării catalizatorilor adecvați, multe metale au fost testate intens: condiția prealabilă pentru adecvare este adsorbția disociativă a azotului (molecula de azot trebuie deci împărțită în doi atomi de azot în timpul adsorbției). În același timp, legarea atomilor de azot nu trebuie să fie prea puternică, altfel capacitățile catalitice ar fi reduse (adică auto-otrăvirea ). Metalele din tabelul periodic al elementelor din stânga grupului de fier prezintă o legătură atât de puternică de azot. Formarea asociată a volumului sau a nitrurilor de suprafață , de exemplu , face catalizatorii de crom ineficienți, se otrăvesc singuri.Metalele din dreapta grupului de fier, pe de altă parte, adsorb azotul într-o mică măsură pentru a putea activa suficient azot pentru amoniac sinteză. Haber însuși a folosit inițial osmiu și uraniu ca catalizatori. Uraniul reacționează la nitrură în timpul catalizei, iar oxidul de osmiu este foarte rar, volatil și foarte toxic.
Datorită prețului său relativ scăzut, a disponibilității mari, a ușurinței de procesare, a duratei de viață și a activității, fierul a fost în cele din urmă ales ca catalizator. Pentru o capacitate de producție de 1800 tone pe zi, de exemplu, sunt necesare o presiune de cel puțin 130 bar , temperaturi de 400 până la 500 ° C și un volum al reactorului de cel puțin 100 m³. Conform studiilor teoretice și practice, scopul pentru îmbunătățirea ulterioară a catalizatorului din fier pur este limitat. Abia în 1984, catalizatorul de fier a fost modificat de cobalt și-a crescut în mod vizibil activitatea.
Catalizatori de a doua generație
Catalizatorii pe bază de ruteniu prezintă o activitate mai mare la presiuni comparabile și la temperaturi mai scăzute și, prin urmare, sunt denumiți catalizatori de a doua generație. Activitatea lor depinde puternic de suportul catalizatorului și de promotori. Un număr mare de substanțe pot fi utilizate ca purtători, pe lângă carbon, aceștia sunt oxid de magneziu, oxid de aluminiu, zeoliți , spinele și nitrură de bor .
Catalizatorii de cărbune activat cu ruteniu au fost folosiți industrial din 1992 în „Procesul avansat de amoniac KBR” (KAAP, german despre procesul de amoniac dezvoltat în continuare conform Kellogg, Brown și Root ). Purtătorul de carbon este parțial descompus în metan , care poate fi redus printr-un tratament special al carbonului la 1500 ° C și, astfel, ajută la prelungirea duratei de viață. În plus, carbonul fin dispersat prezintă un risc de explozie . Din aceste motive și datorită acidității sale scăzute , oxidul de magneziu s-a dovedit a fi o alternativă bună. Purtătorii cu proprietăți acide îndepărtează electronii de ruteniu, îl fac mai puțin reactiv și leagă nedorit amoniacul de suprafață.
Otravuri catalizatoare
Otravurile cu catalizator reduc activitatea catalizatorului. Acestea fac parte din gazul de sinteză sau provin din impuritățile din catalizator în sine, prin care acesta din urmă nu joacă un rol major. Apa, monoxidul de carbon, dioxidul de carbon și oxigenul sunt otrăvuri catalitice temporare. Sulf - fosfor - arsenic - si clor - conexiunile sunt otrăvuri permanente.
Componentele inerte din punct de vedere chimic ale amestecului de gaze de sinteză, cum ar fi gazele nobile sau metanul, nu sunt de fapt otrăvuri catalizatoare, dar se acumulează prin ciclizarea gazelor de proces și astfel reduc presiunea parțială a reactanților , care, la rândul său, are un efect negativ asupra catalizatorului. conversie.
Inginerie de reacție
Condiții de sinteză
Temperatura (° C) | K eq |
---|---|
300 | 4,34 × 10 -3 |
400 | 1,64 × 10 −4 |
450 | 4,51 × 10 -5 |
500 | 1,45 × 10 −5 |
550 | 5,38 × 10 −6 |
600 | 2,25 × 10 −6 |
Sinteza amoniacului are loc la un raport azot / hidrogen de 1 la 3, la o presiune de 250 la 350 bari, la o temperatură de 450 la 550 ° C și folosind α-fierul ca catalizator conform următoarei ecuații:
Reacția este o reacție de echilibru exotermic care are loc cu o reducere a volumului, a cărei constantă de acțiune de masă K eq rezultă din următoarea ecuație:
- .
Deoarece reacția este exotermă, echilibrul reacției se deplasează spre partea amoniacului la temperaturi mai scăzute. Mai mult, patru părți în volum de materii prime produc două părți în volum de amoniac. Prin urmare, în conformitate cu principiul celei mai mici constrângeri , presiunea ridicată favorizează și formarea de amoniac. De asemenea, este necesară o presiune ridicată pentru a se asigura că suprafața catalizatorului este acoperită în mod adecvat cu azot.
De ferită (α-Fe) , catalizatorul este produs în reactor prin reducerea magnetită cu hidrogen. Acest lucru este eficient în mod optim de la temperaturi de aproximativ 400 până la 500 ° C. Bariera de activare pentru clivarea legăturii triple a moleculei de azot este foarte redusă de catalizator , dar sunt necesare temperaturi ridicate pentru o viteză de reacție adecvată. La temperatura de reacție aleasă, optimul se află între descompunerea amoniacului în materiile prime și eficiența catalizatorului. Amoniacul format este îndepărtat continuu din sistemul de reacție. Fracția de volum de amoniac din amestecul gazos este de aproximativ 20%.
Componentele inerte, în special gazele nobile precum argonul , nu trebuie să depășească un anumit conținut pentru a nu scădea prea mult presiunea parțială a reactanților. Pentru a îndepărta componentele gazelor inerte, o parte din gaz este extrasă și argonul este separat într-un sistem de separare a gazului . Extracția argonului pur din gazul de ciclu este posibilă utilizând procesul Linde.
Implementare pe scară largă
Plantele moderne de amoniac produc mai mult de 3000 de tone pe zi într-o singură linie de producție. Următoarea diagramă arată structura unui sistem Haber-Bosch.
În funcție de originea gazului de sinteză, acesta trebuie mai întâi eliberat de impurități precum hidrogen sulfurat sau compuși organici de sulf, care acționează ca otrăvuri catalizatoare. Concentrațiile mari de hidrogen sulfurat, care apar în gazele de sinteză din cocsurile mocnite , sunt îndepărtate într-o etapă de curățare umedă, cum ar fi procesul sulfosolvan , în timp ce concentrațiile mici sunt eliminate prin adsorbție pe cărbune activ . Compușii organosulfurici sunt separați prin adsorbție prin presiune, împreună cu dioxid de carbon, după conversia CO.
Pentru a produce hidrogen prin reformarea aburului, metanul reacționează cu vaporii de apă cu ajutorul unui catalizator oxid de nichel - oxid de aluminiu din reformatorul primar pentru a forma monoxid de carbon și hidrogen . Energia necesară pentru aceasta, entalpia Δ H , este de 206 kJ / mol.
Gazul metan este transformat doar parțial în reformatorul primar. Pentru a crește randamentul de hidrogen și pentru a menține conținutul de componente inerte cât mai scăzut posibil, gazul metan rămas este transformat cu oxigen în monoxid de carbon și hidrogen într-o a doua etapă a reformatorului secundar . În acest scop, reformatorul secundar este încărcat cu aer, azotul necesar pentru sinteza ulterioară a amoniacului pătrunde și în amestecul gazos.
Într-o a treia etapă, monoxidul de carbon este oxidat în dioxid de carbon, care este denumit o conversie a CO sau reacție de schimbare a gazului de apă .
Monoxidul de carbon și dioxidul de carbon se combină cu amoniacul pentru a forma carbamați care, ca solide , ar înfunda rapid conductele și echipamentele . În etapa următoare a procesului, dioxidul de carbon trebuie eliminat din amestecul gazos. Spre deosebire de monoxidul de carbon, dioxidul de carbon poate fi ușor îndepărtat din amestecul de gaze prin spălarea gazelor cu trietanolamină . Amestecul de gaze conține apoi și gaze nobile, cum ar fi argonul și metanul, care sunt inerte .
Amestecul de gaze este apoi comprimat la presiunea de funcționare necesară prin intermediul turbocompresoarelor . Căldura de compresie rezultată este disipată prin intermediul schimbătoarelor de căldură ; este folosit pentru preîncălzirea gazelor brute.
Producția efectivă de amoniac are loc în reactorul de amoniac, prin care primele reactoare izbucnesc sub presiune ridicată, deoarece hidrogenul atomic din oțelul care conține carbon se recombină parțial în metan și produce fisuri în oțel. Acesta este motivul pentru care Bosch a dezvoltat reactoare tubulare, constând dintr-un tub de oțel purtător de presiune în care a fost introdusă o carcasă din fier cu emisii reduse de carbon, în care a fost umplut catalizatorul. Hidrogenul difuzat prin conducta interioară de oțel a scăpat spre exterior prin alezaje subțiri din jacheta exterioară din oțel, așa-numitele găuri Bosch. Dezvoltarea oțelurilor crom-molibden rezistente la hidrogen a făcut posibilă construirea tuburilor cu pereți unici. Un dezavantaj al reactoarelor tubulare a fost pierderea de presiune relativ mare care trebuia reaplicată prin compresie .
Reactoarele moderne de amoniac sunt proiectate ca reactoare de pardoseală cu o pierdere de presiune redusă, în care contactele sunt distribuite ca paturi pe aproximativ zece etaje unul peste altul. Amestecul de gaze curge prin ele unul după altul de sus în jos. Gazul rece este injectat din lateral pentru răcire. Un dezavantaj al acestui tip de reactor este conversia incompletă a amestecului gazos rece în ultimul pat de catalizator.
Alternativ, amestecul de reacție este răcit între straturile de catalizator prin intermediul unor schimbătoare de căldură, amestecul de hidrogen-azot fiind preîncălzit la temperatura de reacție. Reactoarele de acest tip au trei paturi catalizatoare. În plus față de un control bun al temperaturii, acest tip de reactor are avantajul unei conversii mai bune a gazelor din materia primă comparativ cu reactoarele cu alimentare cu gaz rece.
Produsul de reacție este îndepărtat continuu pentru un randament maxim. În acest scop, amestecul de gaze este răcit de la 450 ° C într-un schimbător de căldură folosind apă, gaze proaspăt furnizate și alte fluxuri de proces. Amoniacul se condensează și este separat într-un separator de presiune. Reactanții care nu au fost transformați încă azot și hidrogen sunt comprimați din nou la presiunea de reacție prin intermediul unui compresor de gaz circulant, suplimentat cu gaz proaspăt și alimentat în reactor. Amoniacul este purificat într-o distilare ulterioară.
Produse
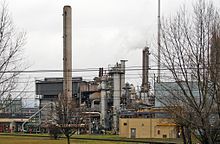
Cea mai mare parte a amoniacului necesar anual este produs utilizând procesul Haber-Bosch. Producția anuală a fost de aproximativ 150 de milioane de tone în 2017 , China , India și Rusia fiind cei mai mari producători. Datorită cerințelor ridicate de energie în producția de hidrogen pur necesar, procesul Haber-Bosch reprezintă aproximativ 1,4% din necesarul de energie din lume . Emisiile de dioxid de carbon generate în acest proces se ridică la aproximativ trei până la cinci procente din emisiile globale, dintre care unele sunt utilizate pentru a genera uree. În zilele noastre, cel puțin în rândul populației națiunilor industrializate, aproximativ 40% din azotul conținut în corpul uman a luat deja parte la sinteza Haber-Bosch.
Aproximativ 80% din produsul primar amoniac este transformat în îngrășământ, alte produse reprezentând 20%. Cele mai importante îngrășăminte cu azot pe bază de amoniac , pe lângă soluțiile gazoase și apoase de amoniac, sunt azotatul de amoniu și ureea .
Producția de uree într-un proces de înaltă presiune se întoarce la Carl Bosch și Wilhelm Meiser și a fost pusă în funcțiune pentru prima dată de BASF în 1922. În 2010 volumul producției a fost de 130 de milioane de tone. Întreaga producție mondială de acid azotic are loc prin arderea catalitică conform procesului Ostwald . Procesul se întoarce la un experiment de prelegere în care un fir de platină strălucitor este scufundat într-un amestec de amoniac și aer pentru a genera gaze azotate . Producția anuală mondială sa ridicat la 80 de milioane de tone în anul 2009. Cel mai frecvent produs secundar al acidului azotic este azotatul de amoniu ; producția anuală în 2002 a fost de aproximativ 39 de milioane de tone, din care aproximativ 80% sunt transformate în îngrășăminte și 20% în explozivi. Alte produse secundare , cum ar fi azotatul de potasiu , fosfați neutralizați parțial sau complet cu amoniac , cum ar fi mono- , di- și polifosfații de amoniu , sulfat de amoniu și soluție de azotat de amoniu-uree sunt frecvent utilizate îngrășăminte.
Aproximativ cinci la sută din producția de amoniac este utilizată pentru a produce explozivi. Grupurile nitro și nitrați găsite în numeroși explozivi se bazează în cele din urmă pe amoniac, care a fost obținut folosind procesul Haber-Bosch, incluzând explozivi importanți precum trinitrotoluen și nitroglicerină . Aproximativ zece la sută din producția de amoniac este utilizată pentru a produce compuși care conțin azot, cum ar fi nitrilii , aminele și amidele . Gama de produse secundare este extrem de diversă și variază de la rășini de uree , sulfonamide la nitrobenzen și produsul său secundar anilină în poliuretan și chimia coloranților, caprolactamă pentru producția de polimeri și până la combustibili pentru rachete, cum ar fi hidrazina .
mecanism
Etape elementare
Mecanismul sintezei amoniacului este împărțit în următoarele șapte etape:
- Transportul materiilor prime de la faza gazoasă prin stratul limită la suprafața contactului
- Difuzia porilor către centrul de reacție
- Adsorbția reactanților
- reacţie
- Desorbția produselor
- Întoarcerea produselor prin sistemul porilor la suprafață
- Reveniți la volumul de gaz.
Datorită structurii învelișului catalizatorului, primele și ultimele două etape sunt rapide în comparație cu adsorbția, reacția și desorbția. Reacțiile de schimb între hidrogen și deuteriu pe catalizatorii Haber-Bosch au loc la o rată măsurabilă chiar și la temperaturi de -196 ° C; Schimbul dintre deuteriu și hidrogen pe molecula de amoniac are loc și la temperatura camerei . Deoarece ambele etape sunt rapide, ele nu pot determina rata de sinteză a amoniacului. Din diverse studii se știe că etapa de determinare a ratei în sinteza amoniacului este disocierea azotului.
Adsorbția azotului pe suprafața catalizatorului depinde nu numai de condițiile de reacție, ci și de structura microscopică a suprafeței catalizatorului. Fierul are fețe de cristal diferite , a căror reactivitate este foarte diferită. Fe (111) și (211) Suprafețele de Fe au de departe cea mai mare activitate. Explicația pentru aceasta este că doar aceste suprafețe au așa-numitele site-uri C7 - acestea sunt atomi de fier cu șapte vecini cei mai apropiați.
Adsorbția disociativă a azotului la suprafață urmează următoarea schemă, unde S * înseamnă un atom de fier pe suprafața catalizatorului:
- N 2 → S * –N 2 (specii γ) → S * –N 2 –S * (specii α) → 2 S * –N (specii β, nitrură de suprafață )
Adsorbția azotului este similară cu chemisorbția monoxidului de carbon. Pe o suprafață Fe (111), adsorbția azotului conduce inițial la o specie γ adsorbită cu o energie de adsorbție de 24 kJmol -1 și o vibrație de întindere NN de 2100 cm -1 . Deoarece azotul este izoelectronic cu monoxid de carbon , acesta se adsorbe într-o configurație on-end în care molecula este legată printr-un atom de azot perpendicular pe suprafața metalică. Acest lucru a fost confirmat de spectroscopia fotoelectronică .
Calculele Ab initio - MO au arătat că, pe lângă σ-Hinbindung , perechea solitară a azotului la metal, o donare π din spate de la orbitalii d este prezentă metalului în orbitalii π * ai azotului care conține fierul- azotul se întărește. Azotul în starea α este legat mai puternic la 31 kJmol -1 . Slăbirea rezultată a legăturii NN ar putea fi demonstrată experimental prin reducerea numărului de undă al vibrației de întindere NN la 1490 cm -1 .
Încălzirea suprafeței Fe (111), care este acoperită de α-N 2 , duce atât la desorbție, cât și la apariția unei noi benzi la 450 cm -1 . Aceasta reprezintă o oscilație metal-N, starea β. O comparație cu spectrele vibraționale ale compușilor complecși permite concluzia că N 2 molecula este legat „side-on“, cu un atom de N în contact cu un site C7. Această structură se numește „nitrură de suprafață”. Nitrura de suprafață este foarte puternic legată de suprafață. La aceasta se adaugă rapid atomii de hidrogen ( reclame H ), care sunt foarte mobili pe suprafața catalizatorului.
Se formează imide de suprafață (NH ad ), amide de suprafață (NH 2, ad ) și amoniacați de suprafață (NH 3, ad ) care au fost detectate prin spectroscopie în infraroșu , acestea din urmă dezintegrându-se cu eliberarea de NH 3 (desorbție). Moleculele individuale au fost identificate sau atribuite utilizând spectroscopia fotoelectronică cu raze X (XPS), spectroscopia de pierdere a energiei electronice de înaltă rezoluție (HREELS) și spectroscopia IR.
Pe baza acestor rezultate experimentale, se poate crea o schemă de reacție care constă din următorii pași individuali:
- H 2 + S * ⇌ 2 H ad
- N 2 + S * ⇌N 2, anunț
- N 2, ad ⇌ 2 N ad
- N ad + H ad ⇌ NH ad
- NH ad + H ad ⇌ NH 2, ad
- NH 2, ad + H ad ⇌ NH 3, ad
- NH 3, anunț ⇌ NH 3 + S *
Ca și în cazul oricărui catalizator Haber-Bosch, etapa de determinare a vitezei în catalizatorii de carbon activat cu ruteniu este disocierea azotului. Centrul activ pentru aceasta în ruteniu este așa-numitul site B 5 , o poziție coordonată de 5 ori pe suprafața Ru (0001), la care doi atomi de ruteniu formează o margine pas cu trei atomi de ruteniu pe suprafața Ru (0001) . Numărul de poziții B 5 depinde de mărimea și forma particulelor de ruteniu, de precursorul de ruteniu și de cantitatea de ruteniu utilizată. Efectul de întărire al purtătorului de bază are același efect ca efectul promotor al metalelor alcaline , care este la fel de important aici ca și în cazul catalizatorului de fier.
Diagrama energetică
Cu cunoașterea entalpiei de reacție a pașilor individuali, se poate crea o diagramă energetică . Cu ajutorul diagramei energetice, reacțiile omogene și eterogene pot fi comparate: Datorită energiei mari de activare a disocierii azotului, reacția omogenă în fază gazoasă nu poate fi efectuată. Catalizatorul evită această problemă, deoarece câștigul de energie care rezultate din legarea atomilor de azot la overcompensates suprafața catalizatorului pentru energia de disociere necesară, astfel încât reacția este în cele din urmă exotermă . Cu toate acestea, adsorbția disociativă a azotului rămâne etapa determinantă a ratei: nu din cauza energiei de activare, ci în principal din cauza factorului pre-exponențial nefavorabil al constantei de viteză. Hidrogenarea este endotermă, dar această energie poate fi aplicată cu ușurință de temperatura de reacție (aproximativ 700 K).
Variante de proces
De la introducerea procesului Haber-Bosch, sinteza amoniacului din azotul atmosferic a devenit unul dintre cele mai importante procese de fabricație chimică din lume. Dezvoltarea variantelor de proces la începutul secolului al XX-lea a servit adesea pentru a eluda revendicările de brevet BASF. Deoarece procesul necesită un consum semnificativ de energie , dezvoltările ulterioare s-au concentrat asupra eficienței energetice . Consumul mediu de energie pe tonă de amoniac în 2000 a fost de aproximativ 37,4 GJ, în timp ce minimul determinat termodinamic este de 22,4 gigajouli pe tonă.
Metoda Casale
Procesul Casale a fost dezvoltat de Luigi Casale la începutul anilor 1920 . Procesul folosește un catalizator de fier, dar funcționează spre deosebire de procesul Haber-Bosch cu o presiune de aproximativ 800 până la 1000 de bari. Acest lucru a făcut reactorul mai mic și a permis un control bun al temperaturii printr-un schimbător central de căldură intern și injecția axială de gaz rece.
Presiunea de funcționare ridicată a permis condensarea directă a amoniacului fără absorbție în apă. Până în 1923 Casale construise 15 fabrici în Europa și Statele Unite cu o capacitate de aproximativ 80.000 de tone de amoniac pe an; în 1927, capacitatea instalată era deja de 320.000 de tone pe an. La acea vreme, Casale era singurul concurent al BASF. În total, peste 200 de plante de amoniac bazate pe prima generație de tehnologie Casale au fost construite în întreaga lume.
Metoda Fauser
Procesul Fauser , numit după inginerul electric italian Giacomo Fauser , a corespuns în mare măsură procesului Haber-Bosch, dar a folosit electroliza apei ca sursă de hidrogen. Celula Fauser folosit forta de 27% soluție de hidroxid de potasiu ca un electrolit și de azbest închise anozi și catozilor , care au asigurat o bună separare a gazelor rezultate. Procesul a fost introdus de Montecatini la începutul anilor 1920 .
Metoda Mont Cenis
Procesul Mont Cenis a fost dezvoltat de Friedrich Uhde și a fost pus în funcțiune pentru prima dată în 1926 la mânăria Mont Cenis . Procesul, cunoscut și sub denumirea de proces de joasă presiune, funcționează la presiuni de 80 până la 90 bari și la o temperatură de 430 ° C. Catalizatorul utilizat a fost un catalizator de cianură de fier-alumină, care a fost mai activ decât catalizatorul dezvoltat de Mittasch. Condițiile mai ușoare ale procesului au făcut posibilă utilizarea oțelurilor mai ieftine pentru construcția reactoarelor.
Procedura AMV
Imperial Chemical Industries a dezvoltat procesul AMV în 1982 cu un catalizator fier-cobalt foarte activ care funcționează la o presiune de reacție de 100 bari și la o temperatură de 380 ° C. Cobaltul în sine nu este activ catalitic, dar servește la stabilizarea contactului prin formarea fazelor de spinel cu oxidul de aluminiu. În plus, atunci când contactul este redus, se formează cristalite de fier mai mici, cu activitate mai mare.
O dezvoltare ulterioară a procesului este procesul LCA (Leading Concept Ammonia) dezvoltat de ICI în 1988, care este conceput pentru debituri mai mici cu același aport de energie. Dioxidul de carbon, care este produs într-o reacție de deplasare apă-gaz într-o singură etapă, este îndepărtat prin adsorbție prin presiune .
Kellogg Advanced Ammonia Process
În 1992, MW Kellog a dezvoltat un catalizator pe bază de cărbune activat cu ruteniu care funcționează la presiuni și temperaturi mai mici sub denumirea Kellogg Advanced Ammonia Process (KAAP). Presiunea necesară este de numai aproximativ 40 bari datorită catalizatorului de ruteniu mai activ, dar mai scump. Metalele alcaline sau alcalino-pământoase precum cesiul și bariul sunt utilizate ca promotori . Se spune că catalizatorul este de aproximativ 10 până la 20 de ori mai activ decât catalizatorul convențional din fier.
Proces de sinteză a amoniacului în stare solidă
În procesul de sinteză a amoniacului în stare solidă ( procesul SSAS, procesul de sinteză a amoniacului în stare solidă ), sinteza electrolitică directă a amoniacului din apă și azot folosind energia electrică ocolește ocolul prin producția de hidrogen din apă. Acest lucru crește eficiența. Formarea amoniacului are loc electrochimic conform următoarei ecuații:
Ecuația brută a reacției este:
Deoarece amoniacul este o substanță cu energie ridicată, este necesară multă energie electrică. Prin urmare, acest proces este economic numai dacă este disponibilă o energie electrică foarte ieftină.
Link-uri web
literatură
- Gerhard Ertl : Etape elementare în cataliza heterogenă. În: Angewandte Chemie . 102, nr. 11, 1990, pp. 1258-1266, doi: 10.1002 / ange.19901021108 .
- Hans-Erhard Lessing : Pâine pentru lume, moarte pentru dușman. în: Stephan Leibfried și colab. (Hg): Wilde Energies din Berlin - portrete din istoria Academiei de Științe Leibniz. de Gruyter, Berlin, 2015, ISBN 978-3-11-037598-5
- Sandro Fehr: „Problema azotului” în economia de război germană din Primul Război Mondial și rolul Elveției neutre . Nordhausen 2009, DNB 993295185 .
- Alwin Mittasch : Istoria sintezei amoniacului. Verlag Chemie, Weinheim 1951, DNB 453395902 .
- Robert Schlögl : Sinteza catalitică a amoniacului - o „poveste nesfârșită”? În: Angewandte Chemie. 115, nr. 18, 2003, pp. 2050-2055, doi: 10.1002 / anie.200301553 .
- Gerhard Ertl, Jens Soentgen : N: Azotul - un element face istoria lumii. oekom Verlag, 2015, ISBN 978-3-86581-736-5 .
- Max Appl: Amoniac. Principii și practică industrială. Wiley-VCH, Weinheim 1999, ISBN 3-527-29593-3 .
- Dietrich Stoltzenberg: Fritz Haber, Carl Bosch și Friedrich Bergius - protagoniști ai sintezei de înaltă presiune . În: Chimia în timpul nostru . bandă 33 , nr. 6 , 1999, p. 359-364 , doi : 10.1002 / ciuz.19990330607 .
Dovezi individuale
- ↑ a b Azot (Fix) - Amoniac. Studiul geologic al SUA, Rezumate despre produsele minerale, ianuarie 2018.
- ^ Vaclav Smil: Ciclul azotului și producția mondială de alimente. (PDF) World Agriculture 2. 9-1., 2011, accesat la 20 februarie 2019 (engleză).
- ^ Fritz Haber: Discurs comemorativ despre Justus von Liebig. În: Jurnal pentru chimie aplicată. 41, 1928, pp. 891-897, doi: 10.1002 / anie.19280413302 .
- ↑ a b c d e f g h Max Appl: Amoniac. În: Enciclopedia lui Ullmann de chimie industrială. Wiley-VCH Verlag, 2006, pp. 11-13, doi: 10.1002 / 14356007.a02 143.pub2
- ^ William Crookes: Discursul președintelui în fața Asociației Britanice pentru Avansarea Științei, Bristol, 1898. În: Știință. 1898, p. 561-575, doi: 10.1126 / science.8.200.561
- ^ William Crookes: problema grâului. Longmans, Green și Co., Londra / New York / Bombay / Calcutta 1917.
- ↑ a b A. Hermann: Haber și Bosch: Pâine din aer - Sinteza amoniacului. În: Physics Journal. 21, 1965, pp. 168-171, doi: 10.1002 / phbl.19650210403
- ^ Nicodem Caro: Industriile cianamidei de calciu și procesele conexe. În: Jurnal pentru chimie aplicată. 22, 1909, pp. 1178-1182, doi: 10.1002 / anie.19090222404
- ↑ John R. Anderson: Cataliză: Știință și tehnologie. Verlag Springer, 1990, ISBN 3-642-64666-2 , p. 48.
- ↑ Hans-Erhard Lessing: Pâine pentru lume, moarte pentru dușman. în S. Leibfried (Hg): Berlins Wilde Energien de Gruyter, Berlin, 2015 p. 349
- ^ Thomas Hager: Alchimia aerului: un geniu evreu, un magnat condamnat și descoperirea științifică care a alimentat lumea, dar a alimentat ascensiunea lui Hitler. Publisher Crown, 2008, ISBN 978-0-307-35178-4 , p. 96.
- ↑ Kristian Birkeland: Despre oxidarea azotului atmosferic în arcurile electrice. În: Tranzacțiile societății Faraday. 2, 1906, pp. 98-116, doi: 10.1039 / tf9060200098
- ↑ Fritz Haber, G. van Oordt: Despre formarea amoniacului în elemente. În: Jurnalul de chimie anorganică. 44, 1905, pp. 341-378, doi: 10.1002 / zaac.19050440122
- ↑ Brevet US971501 : Producția de amoniac. Publicat la 27 septembrie 1910 , inventatori: Fritz Haber, Robert Le Rossignol.
- ↑ Brevet DE235421A : Proces pentru prepararea sintetică a amoniacului din elemente. Publicat la 13 octombrie 1908 .
- ^ A b c d Carl Bosch: Dezvoltarea metodei chimice de înaltă presiune în timpul înființării noii industrii de amoniac. Discurs pentru acordarea Premiului Nobel la 21 mai 1932.
- ↑ Armin Hermann, Charlotte Schönbeck (ed.): Tehnologie și știință (tehnologie și cultură). Springer, 1991, ISBN 3-540-62259-4 , pp. 441-442.
- ↑ Manfred Baerns, Arno Behr, Axel Brehm: chimie tehnică. Manual . Wiley-VCH, 2006, ISBN 3-527-31000-2 , p. 623.
- ↑ a b Alwin Mittasch: Comentarii despre cataliză. În: Rapoarte ale Societății Chimice Germane (Seria A și B). 59, 1926, pp. 13-36, doi: 10.1002 / cber.19260590103
- ↑ Werner Abelshauser, Wolfgang von Hippel, Jeffrey Alan Johnson: The BASF. Din 1865 până în prezent. CH Beck Verlag, 2002, ISBN 3-406-49526-5 , p. 171.
- ↑ David Turnock: Economia Europei de Est, 1800-1989: Etape ale transformării într-o regiune periferică. Routledge Chapman & Hall, 2005, ISBN 1-4039-3287-5 , p. 197.
- ^ Harm G. Schröter: Cartelul internațional al azotului 1929-1939. În: Harm G. Schröter, Clemens A. Wurm (eds.): Politică, economie și relații internaționale, studii despre relația lor în perioada dintre războaiele mondiale . Mainz 1991, ISBN 3-8053-1255-5 , pp. 129-130.
- ^ A b Vaclav Smil: Enriching the Earth: Fritz Haber, Carl Bosch și Transformarea producției mondiale de alimente. MIT Press, 2001, ISBN 0-262-69313-5 , p. 242.
- ↑ Wolfgang Zollitsch: Workers between the Great Depression and National Socialism: a contribution to the social history of the years 1928-1936. Vandenhoeck & Ruprecht, 1990, ISBN 3-525-35751-6 , pp. 22-24.
- ↑ Hans-Erhard Lessing: Robert Bosch. Rowohlt, Reinbek lângă Hamburg, 2007, ISBN 978-3-499-50594-2 , p. 142.
- ^ Azot (fix) - Amoniac - Statistică cerere-ofertă. Studiul geologic al SUA, statistici istorice pentru mărfurile minerale și materiale din Statele Unite, seria de date 140, 2015.
- ↑ a b c d Roman J. Press și colab.: Introducere în tehnologia hidrogenului . John Wiley & Sons, 2008, ISBN 978-0-471-77985-8 , pp. 99-125.
- ↑ Brevet US2083795 : Producția de hidrogen. Publicat la 15 iunie 1937 , inventatori: Georg Schiller, Gustav Wietzel.
- ↑ Vaclav Smil: Enriching the Earth: Fritz Haber, Carl Bosch și Transformarea producției mondiale de alimente. MIT Press, 2001, ISBN 0-262-69313-5 , p. 113.
- ↑ Fangming Jin (Ed.): Aplicarea reacțiilor hidrotermale la conversia biomasei. Springer, 2014, ISBN 978-3-642-54457-6 , p. 221.
- ↑ Friedrich Asinger: Introducere în Petrochimie . Akademie-Verlag, Berlin 1959, p. 138.
- ↑ a b c d e f g h i Max Appl: Amoniac. Principii și practică industrială . Wiley-VCH, Weinheim și colab. 1999, ISBN 3-527-29593-3 , pp. 17–64 ( previzualizare limitată în Căutare de cărți Google).
- ↑ WK Jozwiak, E. Kaczmarek și colab.: Comportamentul de reducere a oxizilor de fier în atmosfere de hidrogen și monoxid de carbon. În: Cataliză aplicată A: Generalități. 326, 2007, pp. 17-27, doi: 10.1016 / j.apcata.2007.03.021
- ↑ Gerhard Ertl: La mecanismul sintezei amoniacului. În: Știri din chimie, tehnologie și laborator. 31, 1983, pp. 178-182, doi: 10.1002 / nadc.19830310307
- ↑ Michael Bowker: doctor în sinteza amoniacului . În: DA King, DP Woodruff (Eds.): Fizica chimică a suprafețelor solide . Volumul 6: Coadsorbție, promotori și otrăvuri . Elsevier, 1993, ISBN 0-444-81468-X , Capitolul 7, pp. 225-268 .
- ↑ a b c d Zhixiong You, Koji Inazu, Ken-ichi Aika, Toshihide Baba: Promovarea electronică și structurală a hexaaluminatului de bariu ca suport catalizator de ruteniu pentru sinteza amoniacului . În: Journal of Catalysis . bandă 251 , nr. 2 octombrie 2007, doi : 10.1016 / j.jcat.2007.08.006 .
- ↑ F. Rosowski, A. Hornung, O. Hinrichsen, D. Herein, M. Muhler: Catalizatori de ruteniu pentru sinteza amoniacului la presiuni ridicate: Pregătirea, caracterizarea și cinetica legii puterii . În: Cataliză aplicată A: Generalități . bandă 151 , nr. 2 aprilie 1997, doi : 10.1016 / S0926-860X (96) 00304-3 .
- ↑ a b Jürgen Falbe: Römpp-Lexikon Chemie (H - L) , Georg Thieme Verlag, 1997, ISBN 3-13-107830-8 , pp. 1644–1646.
- ^ Theodore L. Brown, H. Eugene LeMay, Bruce Edward Bursten, Linda Sue Brunauer (Eds.): Chemistry the Central Science. Ediția a IX-a. Prentice Hall, Upper Saddle River, NJ 2003, ISBN 0-13-038168-3 .
- ↑ a b c A. F. Holleman , E. Wiberg , N. Wiberg : Manual de chimie anorganică . Ediția a 102-a. Walter de Gruyter, Berlin 2007, ISBN 978-3-11-017770-1 , pp. 662-665.
- ↑ Boy Cornils, Wolfgang A. Herrmann, M. Muhler, C. Wong: Cataliza de la A la Z: O enciclopedie concisă. Verlag Wiley-VCH, 2007, ISBN 978-3-527-31438-6 , p. 31.
- ↑ Focus pe chimie, nivel superior, fază introductivă. Cornelsen-Verlag, Berlin 2010, ISBN 978-3-06-013953-8 , p. 79.
- ^ P. Häussinger și colab.: Noble Gases. În: Enciclopedia lui Ullmann de chimie industrială. Wiley-VCH, Weinheim 2006, doi : 10.1002 / 14356007.a17_485
- ↑ E. Leibnitz, H. Koch, A. Götze: Despre procesarea fără presiune a gazului de cocsit de lignit în gaz puternic conform procesului Girbotol. În: Jurnal pentru chimie practică. 13, 1961, pp. 215-236, doi: 10.1002 / prac.19610130315
- ↑ a b Dirk Steinborn: Fundamentele catalizei complexe organometalice. Teubner, Wiesbaden 2007, ISBN 978-3-8351-0088-6 , pp. 319-321.
- ^ A b c Detlef Forst, Maximillian Kolb, Helmut Roßwag: Chimie pentru ingineri. Springer Verlag, 1993, ISBN 3-662-00655-3 , pp. 234-238.
- ↑ Patrick Heffer, Michel Prud'homme: Fertilizer outlook 2010–2014. În: 78a conferință anuală IFA, Paris. 31, 2010, p. 6.
- ↑ Celeste LeCompte: Plantele de îngrășăminte apar pentru a profita de gazul natural ieftin din SUA. În: Scientific American. 2013. (online)
- ↑ TE Crews, MB Peoples: Legume versus surse de azot îngrășăminte: compromisuri ecologice și nevoi umane. În: Agricultură, ecosisteme și mediu. 102, 2004, pp. 279-297, doi: 10.1016 / j.agee.2003.09.018 .
- ↑ Jan Willem Erisman, Mark A. Sutton, James Galloway, Zbigniew Klimont, Wilfried Winiwarter: Cum un secol de sinteză de amoniac a schimbat lumea. În: Nature Geoscience. 1, 2008, pp. 636-639, doi: 10.1038 / ngeo325
- ↑ Brevet US1429483 : Proces de fabricare a ureei. Publicat la 19 septembrie 1922 , inventatori: Carl Bosch, Wilhelm Meiser.
- ↑ a b c d e M. Bertau, A. Müller, P. Fröhlich, M. Katzberg: Industrielle Anorganische Chemie , 2013, Wiley-VCH, ISBN 978-3-527-33019-5 , pp. 31-37.
- ↑ Dirk Steinborn: Fundamentele catalizei complexe organometalice. Teubner, Wiesbaden 2007, ISBN 978-3-8351-0088-6 , p. 7.
- ↑ Allen V. Barker, David J. Pilbeam (Eds.): Manual de nutriție a plantelor . CRC Press, 2006, ISBN 0-8247-5904-4 , p. 40.
- ↑ Jacqueline Akhavan: Chimia explozivilor . Societatea Regală de Chimie, 2011, ISBN 978-1-84973-330-4 , pp. 44-46.
- ^ AF Holleman , E. Wiberg , N. Wiberg : Manual de chimie anorganică . Ediția a 102-a. Walter de Gruyter, Berlin 2007, ISBN 978-3-11-017770-1 , pp. 675-680.
- ^ Walter J. Moore, Dieter O. Hummel: Chimie fizică . Walter de Gruyter, Berlin 1983, ISBN 3-11-008554-2 , p. 604.
- ↑ G. Ertl, SB Lee, M. Weiss: Cinetica adsorbției azotului pe Fe (111). În: Știința suprafeței. 114, 1982, pp. 515-526, doi: 10.1016 / 0039-6028 (82) 90702-6 .
- ↑ a b SB Lee, M. Weiss: Adsorbția azotului pe suprafețele de Fe (111) și (100) promovate cu potasiu . În: Știința suprafeței . bandă 114 , nr. 2-3 , februarie 1982, pp. 527-545 , doi : 10.1016 / 0039-6028 (82) 90703-8 .
- ↑ a b Gerhard Ertl: Reacții la suprafețe solide . John Wiley & Sons, 2010, ISBN 978-0-470-26101-9 , pp. 123 ( previzualizare limitată în căutarea Google Book).
- ↑ Jeppe Gavnholt, Jakob Schiøtz: Structura și reactivitatea nanoparticulelor de ruteniu. În: Physical Review B. 77, 2008, doi: 10.1103 / PhysRevB.77.035404 .
- ^ J. Ruddock, TD Short, K. Brudenell: Integrarea energetică în producția de amoniac. În: Tranzacții WIT pe ecologie și mediu. 62, 1970, doi: 10.2495 / EENV030251 .
- ↑ James A. Kent (ed.): Manualul de chimie industrială și biotehnologie al lui Kent și Riegel . Verlag Springer, 2007, ISBN 978-0-387-27842-1 , pp. 998-999.
- ↑ Brevet US1478550 : Aparat catalitic pentru sinteza amoniacului. Publicat la 25 decembrie 1923 , inventator: Luigi Casale.
- ^ A b Casale SA: Amoniac - Dezvoltarea tehnologiei. Adus pe 27 iunie 2016.
- ↑ Brevet US1495681 : Electrolizator pentru producerea de hidrogen și oxigen. Publicat la 27 mai 1924 , inventator: Giacomo Fauser.
- ↑ Jean Billiter: electroliza tehnică a nemetalelor. Verlag Springer, 1954, ISBN 978-3-7091-5728-2 , pp. 42-44.
- ↑ Bernhard Neumann (Ed.): Manual de tehnologie chimică și metalurgie: I combustibili ramuri anorganice ale industriei. Verlag Julius Springer, 1939, ISBN 978-3-642-92056-1 , pp. 408-409.
- ↑ Huazhang Liu: Catalizatori de sinteză a amoniacului: inovație și practică . World Scientific Pub., 2013, ISBN 978-981-4355-77-3 , pp. 739-740.
- ↑ JR Jennings: Sinteza catalitică a amoniacului. Fundamente și practică. Springer Science and Business Media, 1991, ISBN 1-4757-9594-7 , p. 353.
- ^ Gary Maxwell: Produse sintetice cu azot: un ghid practic pentru produse și procese. Verlag Springer, 2004, ISBN 0-306-48225-8 , pp. 181-182.
- ^ Anne K. Rhodes: nou proces de amoniac, catalizator dovedit în fabrica canadiană. În: Oil and Gas Journal. 47, 1996 (online)
- ↑ Hubert Bielawa, Olaf Hinrichsen, Alexander Birkner, Martin Muhler: Catalizatorul de sinteză a amoniacului din generația următoare: Ruteniu susținut de oxid de bariu. În: Angewandte Chemie International Edition. 40, 2001, pp. 1061-1063, doi : 10.1002 / 1521-3773 (20010316) 40: 6 <1061 :: AID-ANIE10610> 3.0.CO; 2-B .
- ^ Rong Lan, John TS Irvine, Shanwen Tao: Sinteza amoniacului direct din aer și apă la temperatura și presiunea ambiantă. În: Rapoarte științifice. 3, 2013, doi: 10.1038 / srep01145 .